新着情報 山岳トンネル施工におけるずり出し自動化システム「L-CROSSTM」を開発 非GNSS環境下でホイールローダの自律運転を汎用操作機構により実現
2024/07/26
戸田建設(株)(本社:東京都中央区、社長:大谷 清介)は大裕(株)(本社:大阪府寝屋川市、代表取締役社長:飯田 浩二)の協力を得て、山岳トンネル施工におけるずり出し自動化システム「L-CROSSTM:Loading-Construction Robot Operating Systems」を開発し、GNSS※1が利用できない環境下において、汎用の外付け操作機構を用いて「ホイールローダの自律運転」を実現しました(図-1)。
トンネル内では一般的に、自己位置の把握に必要な測位衛星からの電波が届かず、GNSSを利用できません。そのため本システムでは、ホイールローダの上部に設置したLiDAR※2により周囲の状況を把握しながら自己位置を推定します。そして、ホイールローダは、周囲の状況と自己位置の情報を基に、ずり(発破等により破砕された岩石)のすくい上げから、搬出用機械(クラッシャー)に投入するまでの走行ルートを自ら考え、ハンドル等に取り付けた操作機構(図-1)により自律的に走行・動作します。この操作機構は、ホイールローダの機種ごとに異なる内部の制御信号への介入を必要とせず、複数のメーカーや機種に対応可能です。本システムを適用することにより、ずり出し作業の省人化が可能になり、安全性・生産性が向上します。
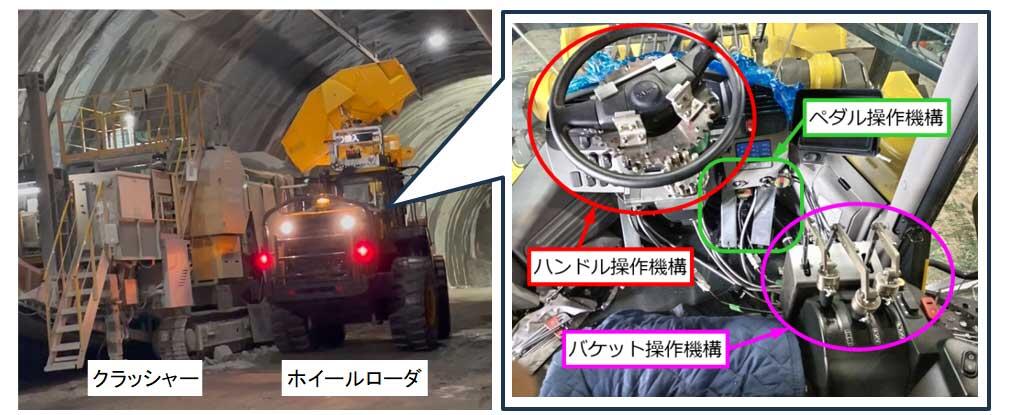
- ※1GNSS:人工衛星を利用して地上の現在位置を計測する衛星測位システムの総称(Global Navigation Satellite System)
- ※2LiDAR:レーザー光を照射して、その反射光の情報をもとに対象物までの距離や対象物の形などを計測する技術
開発の背景
建設業界では、人手不足の解消や労働環境改善を目的に、建設機械の自動化技術の開発が進められています。
当社では山岳トンネルにおける一連の作業の遠隔化・自動化に係わる技術の開発のシリーズ化に取り組んでいます。その一環として、掘削ずり搬出作業の省人化を目指し、GNSSが利用できないトンネル坑内で、ホイールローダの自律運転を可能とする技術の開発を進めてきました。
本システムの概要
山岳トンネル施工のずり出しでは、切羽(トンネル掘削の最先端箇所)の掘削ずりをホイールローダで搬出用機械(ダンプトラックや、クラッシャーとベルトコンベヤの組合せ)に積込み、トンネル外へ搬出します。本システムの開発における、ずりの投入先となる搬出用機械は、位置が固定されていて自律運転が比較的容易となるクラッシャー(大きな岩塊を破砕する機械)とベルトコンベヤの組合せとしました。
本システムは、まず、オペレータが使用開始前にホイールローダに搭乗して、切羽からクラッシャー間を1~2回前後進を行いながら操作し、ホイールローダの上部に設置したLiDARにより作業エリア周辺のマッピングを行います(図-2)。ホイールローダはマッピングにより「ずり」とずりの投入先の「クラッシャー」を認識し、走行ルートの設定(パスプランニング)をして自律運転を開始します。自律運転中は、LiDARにより周囲の状況を把握してトンネル内における自己位置を推定しながら走行し、ずりのすくい上げと投入作業を行います。
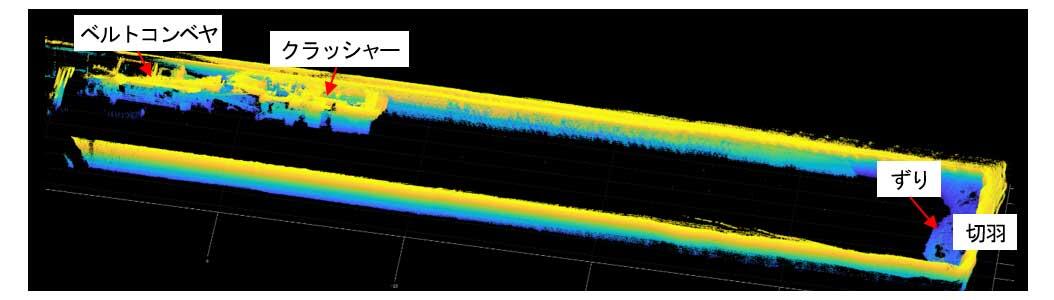
本システムの特徴は下記のとおりです。
- 1ハンドル等に取り付ける外付け操作機構(図-1)は、複数のメーカーや機種に対応可能です。
- 2外付け操作機構には、オペレータの操作と機械の動作を予め学習し、その操作を再現する機能があります。
- 3エンジンの起動・停止、前後進のシフト操作などは、電子制御により行われます。
- 4走行中は、可動部に取り付けられた超音波センサなどの各種センサと三軸傾斜計などの各種計器によって、ホイールローダの動作・姿勢を把握し、これらのデータに基づいてAIが姿勢制御を行います。
- 5ホイールローダのキャビン上部に設置したLiDARで、周囲の点群データを取得し自己位置を推定するため、特別なマーカー等を必要としません。
- 6クラッシャーにもLiDARを設置し、データを連携することでホイールローダの自己位置の推定精度を向上させています。
- 7残りのずり形状から、ずりが多い位置への走行ルートを自律的に設定して向かい、ずりをすくい上げます。
- 8これらの情報は、外部と通信することなくホイールローダに搭載したシステム単体で処理されます。
- 9各種センサによる自動停止機能や外部からの非常停止機能を有しています。
実証施工
実証施工では、掘削中の切羽においてホイールローダの自律運転を試行し、切羽への前進から、ずりのすくい上げ、クラッシャーまでの後進、クラッシャーへのずりの積込みまでの一連の動作が、スムーズに行えることを確認しました(図-1)。
今後の展望
今後は走行データを分析し、熟練オペレータによる操作データを学習させ、AIによる姿勢制御の精度と施工効率の向上を図り、実作業での運用を目指します。さらに、1台ごとに停止位置の異なるダンプトラックへの積込みまで適用範囲を拡大し、山岳トンネル施工におけるずり出しの自動化を推進していきます。